How a microplastic filter got its start in the Bollinger Digital Fabrication Lab
The Penn Libraries' Digital Fabrication Lab served as the epicenter of innovation for the prototype that would launch the startup company Baleena.

Three Penn alumni developed a product as students that has since evolved into a full-blown company — and it all started in the Judith and William Bollinger Digital Fabrication Lab, a resource nestled within the Holman Biotech Commons.
Sarah Beth Gleeson, ENG’22 and Julia Yan, ENG22 (pictured above from right to left) founded the company Baleena with their classmate, Shoshana Weintraub, ENG’22, after the three of them developed a product prototype using the Lab.
“The lab jumpstarted it for us,” Yan says of Baleena.
The evolution of Baleena — a product that emerged from the synergy between a Penn Engineering senior design project and the Digital Fabrication Lab with my guidance as a Computer-Aided Design (CAD) mentor — demonstrates the way CAD programs and 3D printing for rapid prototyping played a pivotal role in turning Baleena from concept into a revolutionary in-washer filter that is now available for preorder.
These passionate Material Science and Engineering students began with a clear mission: to reduce microplastic emissions at their source, drive environmental education and engagement, and reduce the world’s collective plastic footprint. Although their design class provided $500 to get a product off the ground, finding affordable resources to design and test a product was essential.
The Penn Libraries' Digital Fabrication Lab served as the epicenter of innovation for the Baleena project, embodying the essence of the design thinking process. My expertise in CAD programs played a significant role in bringing Baleena’s concept into a tangible reality for testing. The project went beyond technical development; it included educational support for the Baleena team, facilitating their mastery of CAD software. This educational initiative involved personalized instruction that equipped the team with the knowledge and techniques needed to effectively navigate CAD software and 3D printing. These acquired skills formed the bedrock upon which the project was constructed. Leveraging state-of-the-art 3D printing technology, we embarked on a journey of iterative design, fine-tuning and enhancing the prototypes through more than six successive iterations. Each iteration of the project sought to increase waterflow inside the ball so the filter could trap more microplastic particles.
“The fabrication lab really helped us refine our first design. What we started with at the time was something that was kind of like a dryer ball that had these little nubs that let it crawl on clothing,” Yan says.
The product would go through more major design changes in the months that followed, but the dryer ball prototype helped the group achieve their next remarkable feat: winning the President’s Sustainability Prize, which gave the team $100,000 to scale their venture and honored the product’s potential to “make a difference for people and the planet.”
As the Baleena team continued to collect data and push the boundaries of innovation, the product underwent significant transformations. After several stages of testing at the Pennovation Center and work with Nextfab, the dryer ball design evolved into an easy-to-install in-washer filter that intercepts microplastics before they leave the machine. This new design, which is cylindrical in shape, promises to be more efficient and user-friendly.
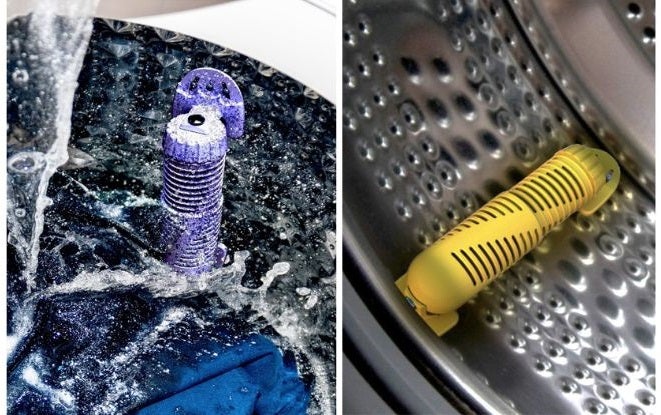
The ongoing transformation of the product mirrors the way Baleena has slowly shifted its focus toward upstream impact. Yan says: “More and more recently, we’re exploring how we work with washing machine manufacturers, like OEMs [original equipment manufacturers]. In that process, we’re trying to better mimic the architecture of the [washing machine] drum. It’s been an evolution of the company over the last two years or so, and we’re still iterating on that,” Yan says.
The journey of Baleena epitomizes the power of collaboration between academic centers, libraries, and passionate individuals. The Penn Libraries' Digital Fabrication Lab not only provided access to state-of-the-art technology but also cultivated an environment where design could flourish. My role as a mentor and educator underscores the critical link between teaching, learning, and real-world application.
“Without the resources that were there, we would have never had enough traction or even just a prototype to show for the President's Prize, which was then the first funding source for us to start this new venture,” says Yan “With $500 and the free resources at the lab, we had the chance to pitch in front of the trustees, and we had tangible proof points to show for it.”
To learn more about Baleena and its mission to combat microplastic pollution, visit their website.
Bollinger Digital Fabrication Lab provides complimentary objects and 3D design consultations contributing to innovation in teaching, learning, research, and clinical care at the University of Pennsylvania. Learn more about 3D printing at the Holman Biotech Commons.
Date
July 31, 2024