Sustainable practices ensure longevity of letterpress equipment, moveable type
All materials used to print, from the type to the printing presses, were made to last for decades, and then recycled or reused.

The Common Press at the University of Pennsylvania is an interdisciplinary typography studio and makerspace dedicated to advancing research and practice in letterpress printing and book arts. Located in the basement of the Fisher Fine Arts Library, we serve students, faculty, staff, and the broader community. Unlike other campus makerspaces such as Education Commons and Biotech Commons, which focus on the most modern printing and rendering technologies, our studio is equipped with antique printing equipment and movable type.
The reuse of material is at the core of letterpress printing, making it an incredibly sustainable craft practice, especially when compared to modern laser, inkjet, or 3D printing. All materials used to print, from the type to the printing presses, were made to last for decades, and then recycled or reused.
Once cast or carved from wood, movable type can last for decades, rearranged by typsetters in different configurations to print words, sentences, and paragraphs. When type is damaged or worn, it is put in a “hell box” to be melted down and cast into new type.
Metal printing presses were made to last for centuries. This is fundamentally different than the mostly plastic desktop printers we use today, most of which have a ten-year life cycle before being discarded in a landfill.
Our printing presses and typefaces are no longer manufactured, and haven't been for decades, so research and maintenance are part of our work at Common Press. We search in old manuals and community listservs to learn how to maintain and repair what we have to the best of our ability.
The first step in this process is identifying what we have in our studio and when it was made. The mystery regarding the equipment's past is common among contemporary letterpress studios, where printers often know only the most recent user of decades-old equipment. Many studios attempt to trace the genealogy of their equipment. At the Common Press, we are just starting to establish where our type and equipment came from. This will help us maintain the equipment.
Our Printing Presses
Historically, research about printing has been focused on what was printed rather than how it was printed. There has been little effort to preserve the legacy of the companies who invented and manufactured the presses we use.
If nothing is known about a printing press, the first step is to locate its brand name and serial number, which will help establish the year of manufacture. Every printing press has a unique serial number cast or etched into its body. Unlike modern serial numbers found on computers, a press's serial number indicates its exact position on the production line. For example, a press with the serial number 14,000 was the 14,000th press manufactured by that company.
At the Common Press, we use four different printing presses almost daily, each with its own history and mechanism.

The oldest press in our collection is a cast-iron Washington Handpress made by R. Hoe & Company with the serial number 6385, acquired via donation from a New Jersey-based print museum. R Hoe & Company made handpresses from 1827 to around 1915. This blog post indicates that serial numbers in the 6000s were made around 1890. Another post by the same researcher states that a handpress with the serial number 6184 was sold from the manufacturer to a shop in Texas in 1905. From this, we assume that our press was made around 1900.
For 400 years, the handpress model was the primary type of press used in letterpress printshops across the western world. The operation of a handpress is not motorized, with no inking rollers. Instead, a team works together to ink the form of type, lay the paper, and operate the press. The printing process is quite slow and labor intensive.
According to the Handpress database, there are currently about 2,300 handpresses in use worldwide, which means more than 5,000 handpresses remain unaccounted for. A large portion of these presses no longer exist, having been sold for scrap metal or otherwise disposed of.
Handpresses fell out of use after the invention of the Gordon press. First patented in 1856, this press features mechanized inking rollers and can be operated by one person, which increases the speed and production of printing. The Gordon Company was acquired by Chandler & Price, who renamed and produced this model of press until 1964.
At the Common Press, we have a Chandler & Price New Press Series 8 x 12, serial number B5933S. The records of the Chandler & Price company were preserved (unlike those of R Hoe & Company), indicating our press is from 1927.
This press was donated by Dr. William C. Stavrides, an alumnus of Penn Dental School who was also an avid printer. Dr. Stavrides’ father ran a commercial job printing shop, and it is possible that he acquired this press directly from the Chandler & Price Company.
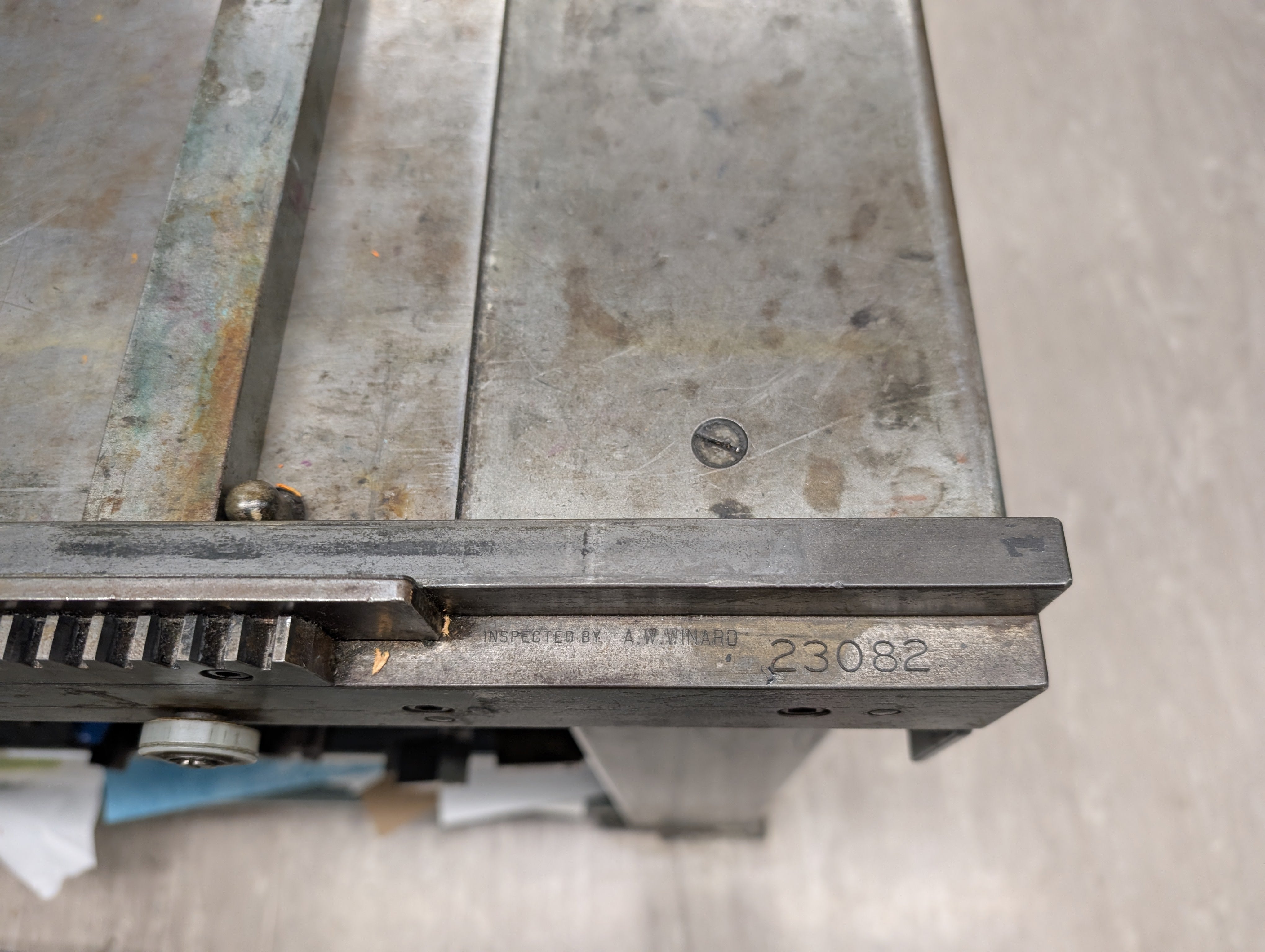
The youngest presses at the Common Press are two Vandercooks, named Binny and Ronaldson in honor of the first type foundry in Philadelphia. These were purchased from Don Black, a prolific reseller and repairer of presses. The Common Press has a Vandercook model Sp-15 (Binny), serial number 23082, made in 1963. The other Vandercook (Ronaldson) is a Number 4 model, serial number 17600, made in 1955.
The Vandercook brand promised excellence when printing text or image. To reinforce this brand, next to the serial number on many presses is the name of the person who inspected the press before it left the factory.
The mechanisms and the body of Vandercook printing press allow for the easy and “perfect” printing of type. These presses were used to produce a few very high-quality prints, which would then be photographed and printed at a large edition using lithographic processes.
The Vandercook Company made presses from 1909 to 1984. Paul Moxon’s census of known serial numbers indicates there are only about 2,616 known Vandercooks in operation worldwide out of the 20,000+ Vandercooks manufactured.
Movable Type
The type library at Common Press holds approximately 300 typefaces, about 25 of which are made of wood, the rest cast in metal. The lineage of metal and wood type is very difficult to establish, as is the manufacture date.
While individual type foundries flourished before the Civil War, most of the large type foundries consolidated into American Type Foundry in 1892. Casting type remained a major part of the U.S. economy until the 1970s, when photo typesetting and offset printing replaced letterpress as the most popular print production methods.
Type can be identified by looking at the shapes and lines of individual printed letters. American Metal Typefaces of the Twentieth Century by Mac McGrew offers the genealogy of specific popular typefaces based on their appearance. But it is very difficult to know when and where a certain type was cast.
At the Common Press, we can trace the history of a few of our typefaces. We know that some portion of the collection was donated by Dr. Stavrides. The cases these typefaces are stored in still bear his family name, as well as his daughter’s name. Users of the collection have mistaken these labels for the names of the type, meaning some typefaces have been mistakenly referred to as “Wendy” and “Stavrides Family” instead of their technical names like Goudy or Garamond.
![]()
|
![]() |
There are three typefaces from the Stavrides donation that are so unique it is easy to identify them as type from the Balto Type Foundry. These fonts are Airport Tourist, Flash, and Onyx. Based out of Baltimore, Balto type designers copied and then slightly altered the design of existing typefaces to make their own versions. Balto Type Foundry was the only place casting these specific fonts, and did so until the late 1970s, after many other foundries had gone out of business.
Repair and Maintenance
There are no certified service professionals for the equipment the Common Press. When a press malfunctions, we rely on a network of online resources and self-taught experts.
For example, our handpress needs a rebuilt frisket, part of the press that holds the paper in place during printing. We’ve begun researching this repair by consulting Richard-Gabriel Rummonds’ book Printing on the Iron Handpress and reaching out to other handpress owners for repair suggestions. Parts will need to be fabricated, and we will research how to install these parts from archival descriptions and images.
We have also started working with the fabrication shop in Penn Engineering to remake a replacement for broken inking disc for one of our tabletop C&P presses.
We send broken type from our hell box to contemporary type foundries to melt and cast new type. Skyline Foundry accepts old type and offers a discount for new type in exchange. Old type is also melted down to make into bullet casings and fishing weights.
Surviving Despite the Odds
The rapid change to digital printing technology in the 1970’s and 80’s meant that old letterpress equipment was quickly deaccessioned to make room for faster and better production. There are many oral accounts of metal type, Vandercook and C&P printing presses being repurposed as boat anchors. Handpresses were also melted down for their iron since the 1800’s.
At Common Press, we do not intend to melt our metal printing presses, however we do take pride in the sustainability of the materials we use. Letterpress printers often joke that our studios will be the only places to print when the internet or power grid fails, meaning we will still be printing through most ecological and world-changing disasters.
Come visit our studio in the basement of Fisher Fine Arts. We offer weekly free workshops in printing and bookbinding to all Penn cardholder, and offer curricular support and team building to interested participants.
Date
October 16, 2024