Learning Through Making: Exploring DIY Bioplastics at the Materials Library
“It’s kind of like making Jell-O.”
Visitors to the Materials Library (housed within the historic Fisher Fine Arts Library) are always excited to learn about our collection of sustainable materials. Products made from petroleum-plastic alternatives — such as shirt buttons made from milk or plastic wrap derived from potatoes — spark the most interest since they appear to be viable solutions to the world’s plastic waste problem. Often, this leads to a common question from our visitors: If something like this exists and is better for the environment, why isn’t this material more widely available? Inevitably, this has also made us wonder whether bioplastics are any more difficult to make than traditional plastics. This is especially difficult to figure out because companies provide little information about the manufacturing process of bioplastic products.
We wanted to make our own DIY bioplastics at an individual scale in order to try to demystify the larger manufacturing processes for ourselves. Lucky for us, there is a good deal of bioplastic activity at Penn.
Assessing opportunities and challenges
Currently, there are a range of commercially available bioplastic materials, from molded cellulose guitar picks mixed with an agar binder, to meadow grass cellulose-based bioplastic flooring. Some products, like polylactic acid (PLA) cutlery largely made from fermented corn, offer the promise of biodegradability over long periods of time but do not entirely remove the more than 30% of additives, like polypropylene and other petroleum-plastics, to stabilize these materials. This incremental approach to supplanting traditional plastics appears to be due, in part, to the negative impact of moisture exposure on the structure of natural materials. Delaying rehydration with coatings, films, or additives is a common practical solution in the current market of bioplastic materials. This became evident in the process of making gelatin-based bioplastics where the gelatin powder is hydrated, heated, and subsequently dried, but more on that later.
Gathering information
Because there are so many different types of materials in our collection, as library staff, we can’t be experts in everything. When it comes to materials like bioplastics, understanding them has always seemed out of reach because we lack either the scientific know-how or firsthand experience with the manufacturing process. However, what we do know are the pathways of finding and accessing information.
While reading books and articles about an object’s “materialness” can only get us so far, another way to learn about a material is through making, which is exactly what we did: we created bioplastics right here at the Materials Library.
Our own adventures into the world of DIY bioplastics were inspired by the efforts of students working at DumoLab Research (DLR), who are creating biomaterials on campus, and from our visits to a class taught by Professor Laia Mogas-Soldevila, Director of DLR, which occurs each semester and explores biomaterials in architecture. She introduced us to a publication distributed by Fab Textiles called Bioplastic Cook Book, which contains several bioplastics recipes.
From the resources we consulted, we were surprised to learn how simple bioplastics were to make. In fact, the entire process is very similar to making Jell-O. A basic recipe only includes three ingredients: water, glycerin, and bio-based coagulant, usually animal gelatin or algae-based agar. All were attainable at the local grocery store or pharmacy. With the ingredients, the process merely involves mixing everything together, boiling the concoction, and then pouring it into a mold or tray where it will be left to cure for several days.
How it all went
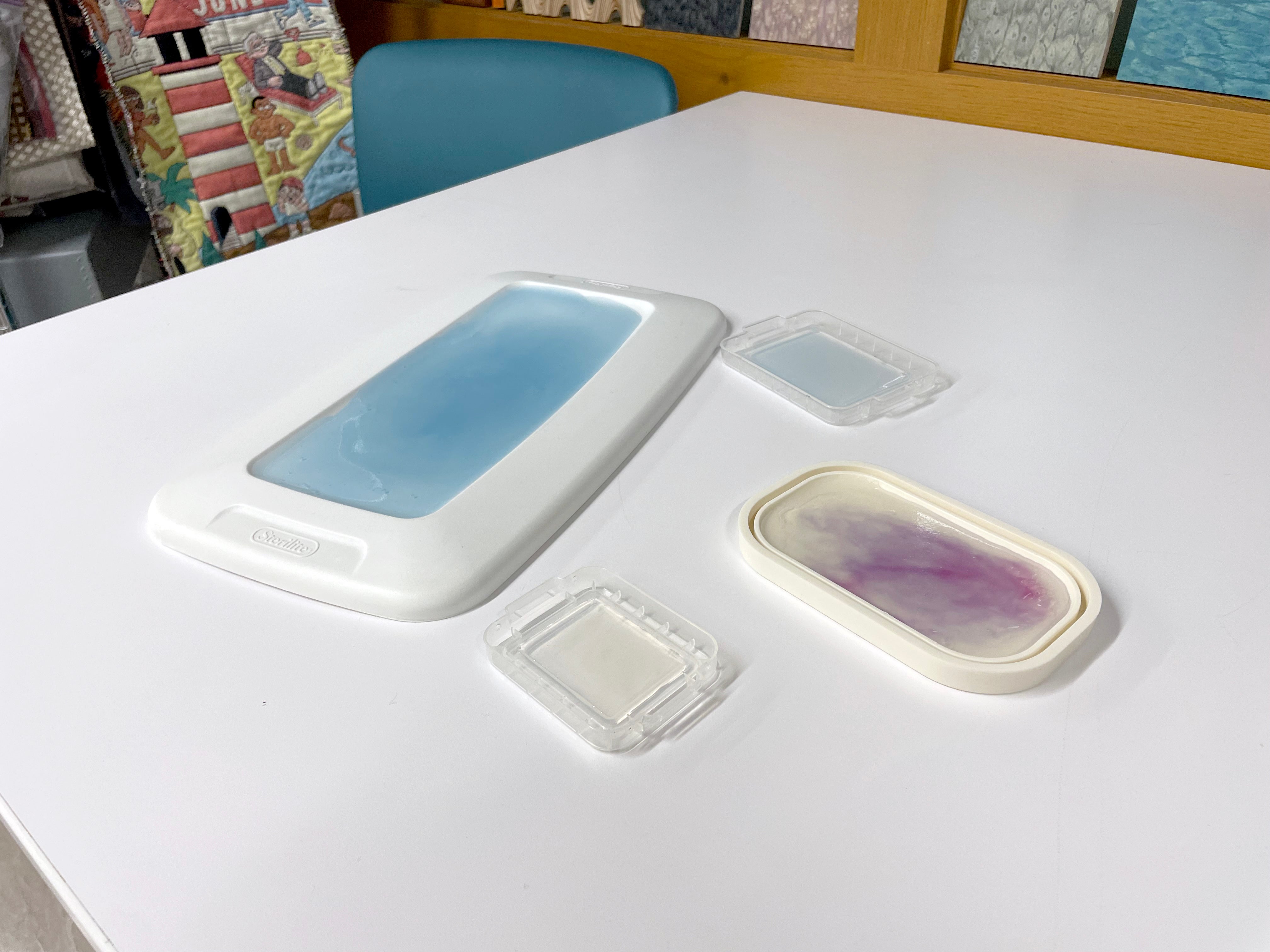
Working within the constraints of the Materials Library space, we aimed to keep things simple. Having read about the possibility of mold growth during the curing process, we wanted to avoid the issue at all costs and aimed to create small, thin samples to speed up the drying time. Armed with a hotplate, a thrift store stockpot, various measuring implements, a couple of plastic trays and lids, and, of course, the basic bioplastic ingredients, we set off to work.
![]() |
![]() |
The first bioplastic we created was gelatin-based. Most of the samples were formed into small rectangular sheets using scavenged plastic container lids. We also tried to create a denser sample, about 1 cm thick, using a plastic container. Just for kicks, we also tossed in some dried orange peels to see if adding decorative elements was possible.
After curing for about four days, our efforts resulted in a fairly convincing, clear, and smooth plastic from the one formed into sheets. To our dismay, the denser sample developed some mold and never cured properly. Needless to say, we tossed that one into the trash.
We also tried creating agar bioplastic. Compared to using gelatin, the process was a little more unwieldy. The agar took longer to dissolve, made the mixture set rather quickly, and took longer to fully cure. The end result was a more rubbery-feeling bioplastic. Guessing the correct amount of glycerin to include in our agar bioplastic concoction was tricky. According to the Bioplastic Cook Book, too little will make the plastic prone to shrinking and brittleness; adding too much could make it harder for the bioplastic to dry.
For our subsequent experiments, we decided to use gelatin because it seemed more forgiving and produced a more reliable result.
Other experiments
Once we were able to dial in on a recipe for creating bioplastic sheets, we tried out different processing techniques to see what type of application might be best for this DIY material. Since bioplastics are meant to be an environmentally friendly alternative to traditional plastics, we wanted to do our best to maintain their biodegradability without introducing non-compostable elements. As referenced earlier, bioplastics are highly water absorbent. With our gelatin-based bioplastic sheet, we noticed that it would warp and begin to dissolve when put in contact with water, making it an ideal biodegradable material. Observing existing forms of single-use plastic products, such as plastic grocery bags and instant noodle packaging, guided us in choosing techniques to try out. In the end, we focused on coloring, laser-cutting, folding, and heat bonding.
![]() |
![]() |
![]() |
![]() |
While the idea of a 100% natural bioplastic was very appealing to us, this proved somewhat difficult to achieve. From our experiments at an individual level, ensuring a completely natural and biodegradable bioplastic was rather resource- and time-intensive. For example, we had originally tried plant-based food coloring but had to switch to synthetic food coloring because plant-based coloring required 10 times the number of drops to achieve a similar level of color. Heat bonding seemed to have a lot of potential in using bioplastic sheets to create 3D forms without introducing additional materials, like glue. However, issues around getting the temperature just right to successfully join two pieces together without burning were too fickle for us to pursue any further.
![]() |
![]() |
Laser cutting, which staff at Education Commons helped us out with, was very promising and we were able to produce some cleanly cut designs from our bioplastic sheets. The simplicity of using folding as a technique also worked really well in turning sheets into different shapes and forms. Ultimately, we went on to explore the potential of folding through origami, which ended up leading to a Materials Library event for Earth Week. All in all, using bioplastic sheets for decorative applications worked the best.
Takeaways
Our foray into making DIY bioplastics changed our expectations about how these types of materials can ease our reliance on petroleum-based plastics and what it means to have a 100% natural alternative. Choosing materials that strike a balance between durability and sustainability is difficult. Nothing we did was close to anything scientific, but our experimentation gave us a more realistic idea about the current state of bioplastics. Most importantly, we quickly saw right away that material exploration through making is a very engaging way to learn. It is as simple as making a batch of unsweetened, unflavored Jell-O.
Date
July 9, 2025